“Nike used predictive-demand analytics to reroute inventory during China store closures and limited sales declines to just 5%.” — Nike
Leading logistics companies make decisions based on data, not guesswork.
Using predictive analytics in logistics helps reduce errors, prevent stockouts, and improve planning accuracy. McKinsey reports that AI-driven forecasting lowers supply chain errors by 20 to 50 percent. Predictive analytics also decreases lost sales and product unavailability by up to 65 percent.
Many businesses still rely on outdated reports and reactive choices. This leads to delivery delays, inventory waste, and unhappy customers.
This guide explains how predictive analytics works in logistics industry, where it adds value, and how to select the right software development partner to build a custom solution for your operations.
For businesses new to this approach, a well-structured predictive analytics guide can help break down the process step by step.
What Is Predictive Analytics in Logistics?
Predictive Analytics in logistics means using real-time and historical data to forecast outcomes such as delivery delays, stock shortages, or customer demand. This approach helps logistics businesses make informed decisions before problems appear.
Think of it like a traffic alert system for your supply chain. For example, if previous trends show delivery slowdowns in a region during holiday weeks, predictive models highlight that risk in advance. If customer demand falls for a specific product, the system recommends adjusting restocks to avoid inventory waste.
The process uses data from shipment records, warehouse movement, weather patterns, and route history. These signals turn into suggestions that help improve planning.
Predictive analytics in the logistics industry gives operations more control, better visibility, and faster decisions. Businesses reduce delays, lower costs, and serve customers with greater consistency.
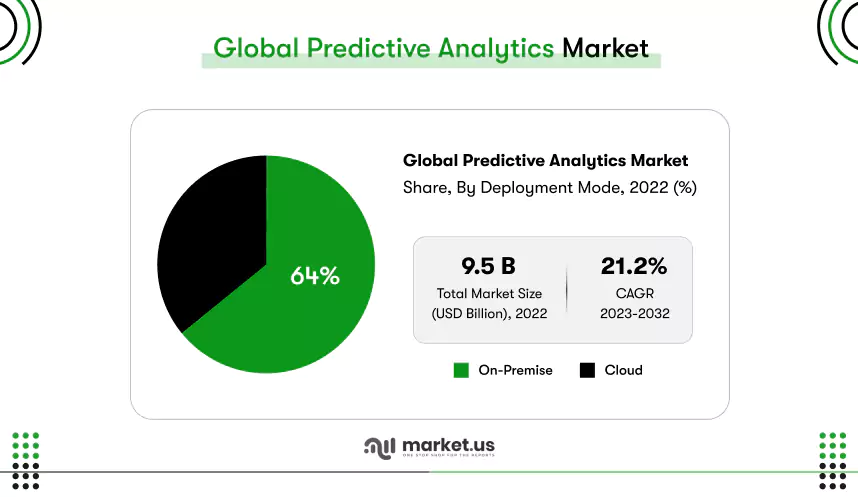
Common Challenges Logistics Businesses Face Without Predictive Analytics
When logistics businesses do not use predictive analytics in logistics, they often face rising costs, poor planning accuracy, and missed customer expectations. Below are the key challenges explained in practical detail.
Missed Deliveries and Reactive Planning
- Logistics teams often discover delivery issues only after customers report them.
- Delays caused by traffic, weather, or internal bottlenecks remain unaddressed until they disrupt fulfillment.
- Without predictive alerts, dispatchers cannot reroute or respond to time-sensitive delays.
- Missed deliveries harm customer trust and affect retention. Predictive analytics in the logistics industry solves this by flagging risks early.
Overstocking or Stockouts
- Poor forecasting leads to either excess inventory or empty shelves.
- Overstock consumes warehouse space, ties up capital, and causes losses when goods expire.
- Stockouts delay orders and damage relationships with key clients.
- With predictive analytics in logistics, businesses forecast demand by region and season to maintain ideal inventory levels.
Unplanned Costs from Emergency Shipments
- Reactive logistics results in higher costs for expedited freight and emergency staff allocations.
- These costs reduce margins and often arise due to avoidable planning gaps.
- Last-minute problem-solving also burns team productivity and time.
- Accurate forecasting allows teams to plan ahead and reduce operational volatility.
Poor Visibility Across the Supply Chain
- Many logistics businesses operate with siloed data and outdated reports.
- Leaders cannot track warehouse loads, vehicle status, or delivery timelines in real time.
- These blind spots prevent proactive decisions and delay recovery during disruptions.
- How to use predictive analytics in logistics starts by centralizing live data into dashboards that support smarter actions.
Rigid and Inefficient Route Planning
- Fixed route schedules do not account for traffic patterns, fuel pricing, or delivery urgency.
- This leads to higher fuel use, increased delivery times, and wasted vehicle capacity.
- Inefficiency at this level compounds across every shipment.
- Predictive models create optimized routes tailored to day-to-day operating conditions.
Delayed Response to External Disruptions
- Teams often act too late when facing supplier issues, port delays, or demand spikes.
- Without early warning, businesses miss opportunities and struggle with cost recovery.
- Manual systems and slow reporting tools cannot adapt in real time.
- Benefits of predictive analytics in logistics include proactive alerts that support faster, more confident decisions.
Each of these challenges eats into profit, slows down operations, and damages customer trust. Businesses that continue without predictive analytics in logistics will always stay reactive, not strategic. But companies that invest in predictive analytics for supply chain gain control, reduce risk, and build logistics systems that grow with demand.
How Predictive Analytics in Logistics Works Across Systems and Operations
Predictive analytics in logistics works by transforming raw operational data into accurate forecasts and clear business actions. This happens through a combination of backend data processing and frontend system responses. Below is a practical breakdown of how predictive analytics works, step by step.
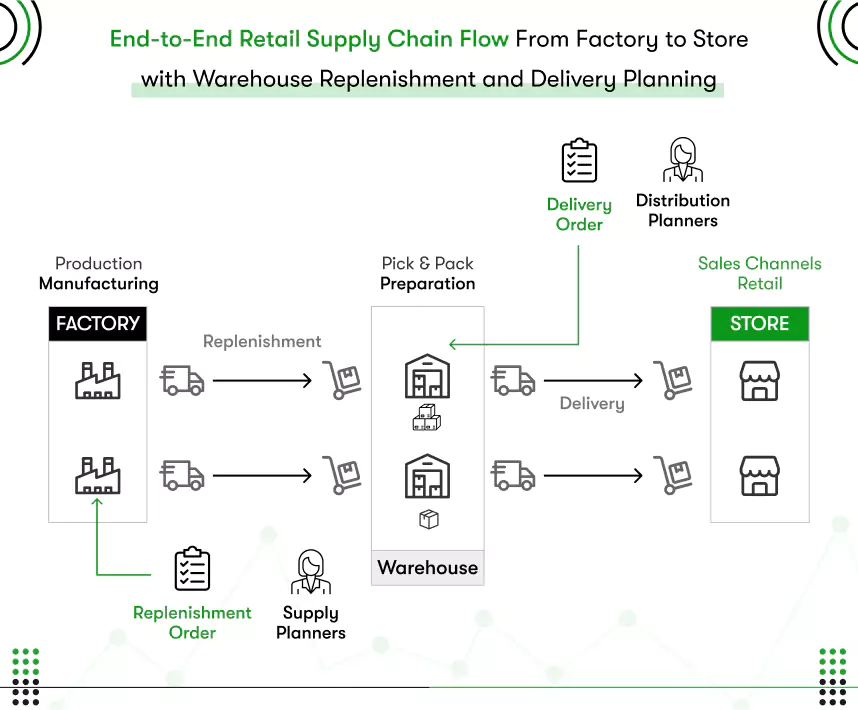
Step–1: Collect Data from All Touchpoints (Backend)
- Logistics systems collect data from order history, delivery timelines, vehicle logs, inventory levels, and warehouse scans.
- External data sources such as weather forecasts, traffic APIs, and fuel cost trackers also feed into the pipeline.
- Cloud-based storage systems like AWS, Azure, or Google Cloud store this information securely for real-time access.
- The backend ensures that predictive analytics in logistics industry receives live and historical data for high-quality predictions.
Step–2: Clean and Structure Data for Accuracy (Backend)
- The system removes duplicate entries, fixes missing values, and normalizes units and formats.
- Feature engineering adds new fields like “stockout frequency,” “average delay by zone,” or “fuel cost per route.”
- This clean, structured dataset becomes the foundation for accurate machine learning models.
- High-quality data directly improves the reliability of predictive outcomes.
Step–3: Train Forecasting Models Based on Your Business Data (Backend)
- Data scientists choose algorithms such as time series forecasting, regression models, or neural networks based on the use case.
- The models are trained using labeled data to learn patterns and relationships between supply chain variables.
- For example, the system may learn how demand changes by weekday, or how delivery time varies by region.
- This process creates the core engine that powers predictive analytics for logistics applications.
Step–4: Deploy the Prediction Engine into Your Live Systems (Backend)
- Once trained, the model is deployed using APIs and microservices that run in your live production environment.
- Predictive analytics processes real-time inputs from your systems and returns updated forecasts regularly.
- This engine can forecast delivery delays, suggest ideal inventory levels, or flag risky shipments before issues occur.
- All forecasts are stored and made available to frontend tools for visibility and action.
Step–5: Display Predictions Using an Operational Dashboard (Frontend)
- Frontend interfaces are built using frameworks like React or Angular and designed for easy use by your logistics team.
- The dashboard displays clear, actionable insights such as “Warehouse X will overstock in 4 days” or “Driver Y is likely to miss the delivery window.”
- Users can filter by warehouse, shipment, or region to see forecasts relevant to their task.
- These dashboards are the face of predictive analytics in logistics, delivering usable insights in seconds.
Step–6: Trigger Automated Responses and Workflows (Frontend + Backend)
- Forecasts connect to business rules in your software to automate key decisions.
- If a shipment shows a 75% risk of delay, the system may reroute it or alert dispatch.
- If predicted demand exceeds capacity, the software may increase orders or shift stock automatically.
- This automation reduces human error and speeds up decision-making across the logistics workflow.
Step–7: Monitor Accuracy and Improve the Models Over Time (Backend)
- The system tracks the accuracy of each prediction and collects feedback from real-world outcomes.
- Machine learning models retrain on this updated data to adapt to new patterns.
- This continuous improvement loop ensures your forecasts remain reliable as conditions change.
- The benefits of predictive analytics in logistics grow over time as the models become more intelligent.
Each layer of this process, from backend data handling to frontend automation, plays a critical role. When built correctly, a custom solution using predictive analytics in logistics enables faster decisions, fewer disruptions, and complete control over operations at scale.
Key Use Cases of Predictive Analytics in Logistics That Solve Real Business Problems
Predictive analytics in logistics helps companies prevent delays, reduce cost per shipment, and plan smarter across every supply chain layer. Each use case listed below solves a specific business problem that logistics teams in the USA, UK, and UAE face every day.
Demand Forecasting
- Predictive models analyze sales trends, seasonality, and order frequency to forecast product demand by region.
- Teams can avoid both overstocking and stockouts by stocking the right quantity at the right location.
- Forecasting helps procurement and warehouse planning align with real market behavior.
- This use case directly improves inventory turnover and working capital. Predictive analytics in the logistics industry depends on accurate demand signals.
Route Optimization
- AI models evaluate real-time traffic, historical delays, and weather to recommend the most efficient delivery routes.
- Dispatch teams use route predictions to reduce travel time, fuel consumption, and late deliveries.
- Routes can be adjusted daily based on volume, region, or priority orders. While routing is optimized in real time, AI for demand forecasting in thse logistic helps teams plan ahead by predicting order volumes and inventory needs across each zone.
- This technique improves delivery speed and reduces operational cost per shipment.
Warehouse Space and Labor Planning
- Predictive systems forecast incoming and outgoing stock to plan storage allocation in advance.
- Teams can prepare labor shifts and docking schedules based on forecasted warehouse loads.
- This helps avoid congestion, overtime costs, and space mismanagement.
- How to use predictive analytics in logistics starts with using forecasts to plan space and manpower accurately.
Fleet Maintenance Prediction
- IoT devices and vehicle logs provide real-time condition data to machine learning models.
- These models predict component failure, maintenance schedules, and downtime risk before breakdowns occur.
- Maintenance teams schedule repairs based on usage, not fixed timelines.
- This reduces unexpected breakdowns and extends vehicle lifespan. Benefits of predictive analytics in logistics include lower repair costs and better fleet availability.
Delivery Delay Risk Management
- Predictive models track delivery history, route issues, weather conditions, and driver performance.
- The system flags shipments with high delay probability before the delay happens.
- Operations managers can reroute or prioritize these shipments to meet service levels.
- This keeps customers informed and improves delivery reliability.
Supplier Reliability Scoring
- Predictive analytics models score suppliers based on historical delivery performance, defect rates, and response time.
- Procurement teams use these scores to adjust vendor allocations and reduce fulfillment risk.
- This helps maintain a consistent inbound supply chain with fewer disruptions.
- Predictive analytics in logistics helps businesses build stronger supplier networks through reliable data, not assumptions.
Every use case in this section solves a real operational challenge. Businesses that adopt predictive analytics in logistics reduce waste, improve speed, and gain better control across their supply chain.
The Process to Build a Custom Predictive Analytics Solution for Logistics Operations
Custom software built with predictive analytics in logistics solves specific operational problems like delivery delays, inventory issues, or poor route planning. This section explains how logistics businesses move from identifying a need to launching a fully functional predictive system, step by step.
Step–1: Define a Logistics Problem with Measurable Impact
- Start by identifying a clear challenge such as missed deliveries, stockouts, or unplanned freight costs.
- Set measurable goals like reducing shipment delays by 25% or cutting excess inventory by 20%.
- A focused problem helps your software partner build a solution that delivers real results.
- This is the foundation of a successful predictive analytics in logistics project.
Step–2: Choose a Custom Software Partner with Logistics Expertise
- Select a team with experience in machine learning, logistics tech stacks, and workflow-based system design.
- Ask for case studies or proof of work in route optimization, demand forecasting, or WMS/TMS integration.
- A qualified partner reduces development risk and accelerates time-to-value.
- Strong collaboration begins with domain understanding, not just coding ability.
Step–3: Share Your Existing Systems and Data Availability
- Provide access to your ERP, order management, fleet tracking, and inventory systems.
- Discuss which data points you already collect, where they’re stored, and how often they update.
- Your partner will audit what’s usable, what’s missing, and what needs cleaning.
- A full data picture supports effective predictive analytics in logistics industry outcomes.
Step–4: Build a Roadmap Around Your Most Valuable Use Case
- Define the first version of your solution, and ideally one use case like demand forecasting or delay risk alerts.
- Align timelines, delivery phases, and KPIs with your internal teams.
- Plan for testing, iteration, and eventual scaling to other workflows.
- A clear roadmap ensures business alignment throughout the build process.
Step–5: Develop and Test in Agile Sprints
- Your partner will design, build, and test features in short development cycles.
- Each sprint includes working demos, testing rounds, and feedback sessions with your internal stakeholders.
- You stay involved throughout, validating the direction and performance at each stage.
- This process keeps the solution focused on real operational needs.
Step–6: Launch and Embed the Solution into Daily Operations
- Once approved, the predictive solution goes live and becomes part of your logistics workflows.
- Dashboards, alerts, and triggers are integrated with your current systems and team routines.
- Onboarding sessions ensure warehouse, dispatch, and planning teams use the insights correctly.
- How to use predictive analytics in logistics becomes clear when predictions guide everyday actions.
Step–7: Measure Performance and Expand Over Time
- Track outcomes using live KPIs: fewer stockouts, faster deliveries, and lower shipment costs.
- Work with your partner to refine models based on real feedback and operational shifts.
- Plan expansions across new warehouses, countries, or product categories.
- The benefits of predictive analytics in logistics grow as your system evolves with your business.
Every step in this process turns predictive technology into a working business asset. With the right partner, custom software built using predictive analytics in logistics helps solve your most pressing challenges while creating long-term operational value.
A team experienced in logistics app development ensures that your solution aligns perfectly with your workflows, systems, and growth goals.
How to Choose the Right Software Development Partner for Predictive Analytics in Logistics
The success of any solution using predictive analytics in logistics depends on the software partner you choose. A capable partner does more than write code. They understand logistics, know your challenges, and can design systems that deliver business outcomes. Below are the must-have traits to look for when hiring a development team.
Proven Experience in Logistics and Supply Chain Systems
- Look for partners who have built custom solutions for transportation, warehousing, or inventory-heavy businesses.
- Ask if they have experience working with TMS, WMS, or ERP integrations.
- Review case studies and ask for live demos.
- Domain experience reduces trial and error and speeds up delivery.
- A logistics-aware team builds better predictive analytics in logistics industry applications.
Capability to Work with Your Data Sources
- Your partner must know how to connect and normalize data from your systems and third-party tools.
- This includes ERP, order tracking systems, IoT sensors, and fleet management platforms.
- Ask how they handle unstructured or inconsistent data.
- A team skilled in data engineering will ensure accurate forecasting and faster insights.
Strong ML and AI Development Expertise
- Make sure your partner can build and deploy predictive models, not just reports and dashboards.
- They should have a working command of time series forecasting, classification models, and optimization logic.
- Check if they’ve worked with Python, TensorFlow, or scikit-learn in real-world projects.
- Predictive analytics for logistics depends on accurate and retrainable models, not static algorithms.
Focus on Business Outcomes, Not Just Technology
- A great partner focuses on reducing your delivery delays or inventory waste, not just deploying features.
- They must ask about KPIs, operational pain points, and team workflows before development begins.
- This mindset ensures your solution drives value from day one.
- How to use predictive analytics in logistics depends on mapping tech outcomes to business impact.
Agile Process and Transparent Collaboration
- The team should offer sprint-based delivery with regular updates and working demos.
- You should always know what is being built, tested, or changed. This reduces risk and keeps the solution aligned with your business goals.
- For features like last-mile delivery with predictive analytics, close collaboration is essential to ensure the system adapts to live conditions and customer expectations.
- Look for collaboration tools like Jira, Notion, or Slack to stay in sync.
Support After Deployment
- Predictive systems need monitoring, feedback loops, and model tuning after launch.
- Choose a partner who offers ongoing support, not just project delivery.
- Ask about model retraining cycles, performance reviews, and versioning policies.
- The benefits of predictive analytics in logistics only grow with long-term optimization.
The wrong partner builds software that looks good but solves nothing. The right partner delivers a solution using predictive analytics in logistics that reduces delays, lowers costs, and fits your operations from day one. Choose the team that understands your business, not just your code.
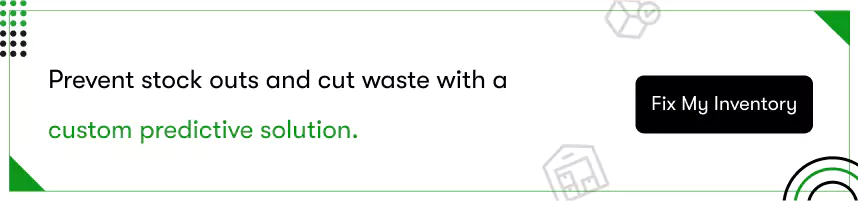
Success Metrics to Track After Implementing Predictive Analytics in Logistics
Once a system using predictive analytics in logistics goes live, measuring impact becomes critical. Tracking the right metrics helps you prove ROI, tune the models, and guide future improvements. Below are the most important KPIs logistics businesses should monitor after implementation.
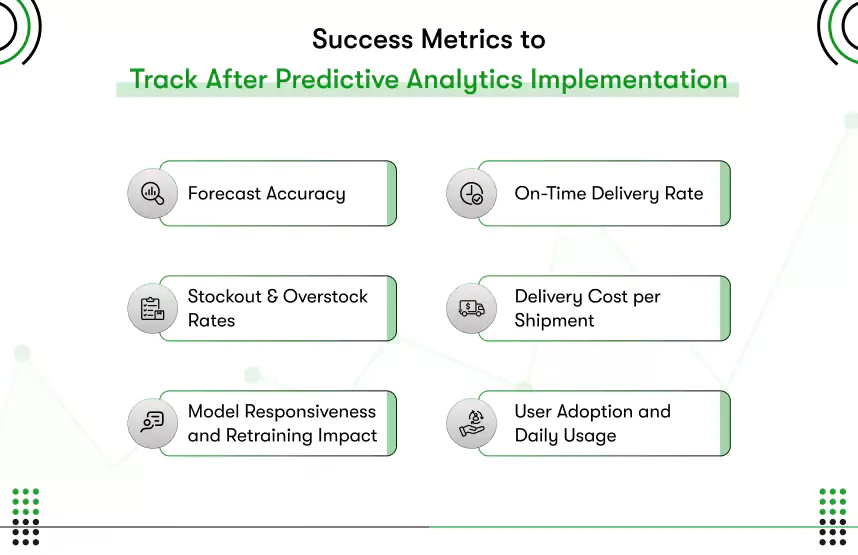
Forecast Accuracy
- Measure how close the predicted demand, stock levels, or delivery times are to actual outcomes.
- A model that consistently predicts within 10–15% accuracy signals strong data quality and model performance.
- Low accuracy means your data or logic needs adjustment.
- This metric forms the foundation of trust in predictive analytics in logistics industry systems.
On-Time Delivery Rate
- Track the percentage of orders delivered within the expected window.
- Higher on-time rates signal that your predictive routing and risk alerts are working.
- Delays that used to be reactive now get handled proactively.
- This improves service-level agreements and customer satisfaction.
Stockout and Overstock Rates
- Monitor how often products go out of stock or remain overstocked across distribution centers.
- Effective predictive inventory planning reduces both risks at the same time.
- Balanced inventory means lower carrying costs and higher order fulfillment rates.
- This is one of the core benefits of predictive analytics in logistics.
Delivery Cost per Shipment
- Calculate your average delivery cost before and after predictive implementation.
- Reduced costs signal improvements in route planning, load optimization, and fewer emergency shipments.
- You can also compare fuel usage and driver time metrics.
- Cost savings validate the operational efficiency of your predictive models.
Model Responsiveness and Retraining Impact
- Measure how often your model is retrained based on new data and operational feedback.
- Track improvements in accuracy or reliability after each retraining cycle.
- A well-maintained model adapts as your business changes.
- This reflects how well you use predictive analytics for logistics as a living system, not a static tool.
User Adoption and Daily Usage
- Monitor how frequently your teams use the dashboards, alerts, or automated features.
- High usage rates show that the solution is embedded in daily decisions.
- Low adoption signals poor training, irrelevant alerts, or dashboard clutter.
- Predictive systems only create impact when the right people use them every day.
In particular, warehouse management with predictive analytics requires consistent usage to ensure inventory decisions, staffing, and storage plans align with real-time demand.
Tracking the right metrics is not optional. It is the only way to measure whether your solution using predictive analytics in logistics is actually improving delivery speed, cost, and decision-making across your operations.
Case Studies: Predictive Analytics in Logistics Delivering Real Results
Leading logistics companies use predictive analytics in logistics to solve real problems like delayed shipments, high fuel costs, and stock imbalances. The case studies below show how global brands implemented predictive systems and achieved measurable improvements across cost, delivery speed, and operational reliability.
1. Nike: Limiting Sales Decline During Store Closures
- Nike combined RFID tracking with predictive-demand analytics to manage inventory during China’s store closures.
- The system routed goods from physical stores to online channels ahead of disruptions.
- This reduced excess stock and ensured availability where it mattered most.
- As a result, Nike limited sales decline to just 5% in China—while many competitors saw much larger drops.
- This example shows how predictive analytics in logistics can directly protect revenue during unforeseen disruptions.
2. UPS: Saving $400 Million with Route Optimization
- UPS developed ORION, a predictive route planning system using live data and historical route trends.
- The system recalculates daily delivery paths based on fuel costs, traffic, and package volume.
- With better routing decisions, UPS saved 10 million gallons of fuel annually.
- The company reported up to $400 million in cost savings from this system.
- This shows how predictive analytics for logistics creates immediate cost impact while improving service quality.
Nike reduced sales loss. UPS cut millions in fuel and routing costs. These outcomes came from using predictive analytics in logistics with a tailored system built around real business goals. Logistics companies that invest in custom predictive solutions improve accuracy, reduce waste, and gain a long-term competitive edge. Route optimization using predictive analytics plays a major role in these outcomes by helping teams plan faster, smarter, and more cost-effective delivery routes.
How Much Does It Cost to Implement Predictive Analytics in Logistics?
The cost of building a custom solution using predictive analytics in logistics depends on the use case, complexity, and system integration. Below is a realistic breakdown based on mid-sized logistics businesses.
MVP or Single Use Case Solution
- A delivery delay prediction tool or basic demand forecasting system costs between US $40,000 and US $80,000.
- This includes backend data integration, model development, and a usable dashboard for daily operations.
- The goal of this setup is to validate value before expanding into more features.
- Starting with one use case helps logistics businesses deploy predictive analytics in logistics industry with minimal risk.
Moderate-Scale Custom Implementation
- A system covering route optimization, inventory forecasting, and maintenance alerts typically costs US $80,000 to US $150,000.
- This estimate includes integrations with internal tools like ERP, WMS, and TMS.
- Teams also receive custom interfaces and alert systems built for real-time decisions.
- This scope suits logistics businesses managing multi-region or multi-warehouse operations.
Ongoing Maintenance and Optimization
- Annual support, model updates, and performance monitoring cost between US $10,000 and US $25,000.
- Predictive models evolve over time based on new data and operational patterns.
- Continuous maintenance ensures that the system adapts to changing business needs.
- Long-term accuracy is a core part of successful predictive analytics for logistics implementation.
Every project is different, but realistic predictive analytics solutions typically start under US $100,000. Logistics companies that invest in the right problem, the right scope, and the right team often recover that cost through savings in routing, delivery timing, and inventory handling within the first 12 to 18 months.
When paired with predictive maintenance for delivery, these systems also help reduce vehicle downtime and avoid last-minute disruptions, adding even more value over time.
When Should You Invest in Predictive Analytics in Logistics?
Logistics teams often ask when the right time is to implement predictive analytics in logistics. The answer depends on business needs, operational maturity, and available data. Below are the most common and practical indicators that show your logistics business is ready for a predictive system.
Delays and Cost Overruns Are Increasing
- Delivery performance is inconsistent and your operations team often reacts after the problem occurs.
- Emergency shipments and overtime payouts are rising quarter by quarter.
- These costs suggest a clear need for predictive routing and demand-based planning.
- This is where predictive analytics in the logistics industry delivers immediate value.
Inventory Is Either Overstocked or Frequently Out of Stock
- Your warehouses have high storage costs from excess stock or repeated shortages of fast-moving SKUs.
- The planning team struggles to balance supply across regions or channels.
- A demand forecasting model can reduce both extremes by predicting product movement more accurately.
You Have Disconnected Systems That Cannot Talk to Each Other
- Your ERP, WMS, and fleet systems are not integrated and work in silos.
- Teams spend hours pulling reports manually instead of making decisions.
- A custom solution with predictive analytics can unify data and automate insights across departments.
- This improves decision-making speed and reduces errors.
Your Business Is Expanding and Complexity Is Growing
- You are adding warehouses, SKUs, new delivery zones, or cross-border shipping.
- Manual planning is no longer enough to manage complexity at scale.
- Predictive systems adapt faster as operations expand and patterns shift.
- How to use predictive analytics in logistics becomes essential during scaling phases.
You Already Collect Data but Do Not Use It Effectively
- Your business tracks delivery times, stock movement, or fuel usage, but does not convert that data into action.
- You have the data but lack the models to extract value from it.
- Predictive tools can turn unused data into accurate decisions that improve daily operations.
You Have Reached Operational Limits with Current Tools
- Excel sheets, static reports, or legacy planning tools are no longer keeping up.
- Decision-making is slow and disconnected from real-time field conditions.
- Predictive models offer automated insights based on live data inputs.
- This reduces dependency on outdated methods and improves forecasting accuracy.
If your team is dealing with late shipments, poor inventory balance, or planning inefficiencies, now is the right time. A solution built using predictive analytics in logistics helps you solve these problems before they grow and keeps your operations aligned with real-time demand.
Working with a team that offers logistics predictive analytics consulting ensures your system is tailored to your specific challenges and built for measurable business outcomes.
Conclusion
Logistics teams that rely on manual planning and outdated tools face growing delays, high costs, and lost business. Companies using predictive analytics in logistics gain speed, visibility, and control across every supply chain function. Forecasts replace guesswork. Smart routing replaces static routes. Inventory stays balanced without overstock or shortages.
Kody Technolab helps logistics businesses build custom predictive solutions tailored to real operational goals. As a company specializing in logistics software development services, our team handles everything from connecting your existing systems to building AI models and designing clean, user-friendly dashboards. You receive a system built for your workflow, not a one-size-fits-all product.
Decisions become faster. Shipments move smarter. Forecasts turn into competitive advantages.
If your operations are growing or your costs are rising, now is the time to act. Kody Technolab is ready to design your predictive solution with full-stack development and long-term support.
Let’s build your logistics advantage with predictive analytics. Talk to our team today.
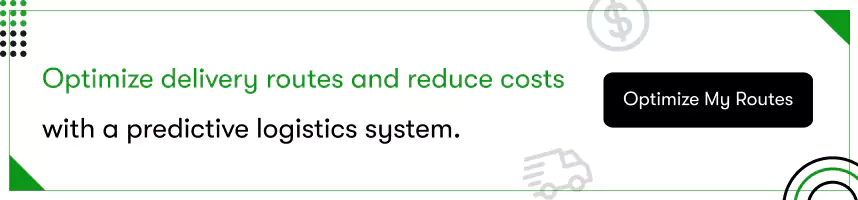